Spis treści
Czym są podkładki sprężyste?
Podkładki sprężyste odgrywają istotną rolę w połączeniach śrubowych. Ich zasadniczym zadaniem jest poprawa wytrzymałości oraz zapobieganie luzowaniu, co jest szczególnie ważne w wielu aplikacjach inżynieryjnych. Te elementy działają niczym sprężyny, dostosowując się do drgań i zmieniających się obciążeń, co pozwala na utrzymanie stabilnej siły docisku. Dzięki swojej elastyczności, podkładki skutecznie kompensują wibracje, co wpływa na niezawodność połączeń.
W szczególności, podkładki zgodne z normami DIN 127 oraz PN 82008 cieszą się uznaniem ze względu na doskonałą elastyczność i wysoką odporność na zmęczenie materiału. Znajdują one zastosowanie głównie w:
- przemyśle motoryzacyjnym,
- maszynowym,
- budowlanym,
gdzie solidne mocowanie elementów ma kluczowe znaczenie. Dzięki swojej funkcji, podkładki sprężyste nie tylko zapobiegają luzowaniu w połączeniach gwintowanych, ale również przyczyniają się do wydłużenia żywotności złączy oraz zwiększają bezpieczeństwo w operacjach mechanicznych.
Podczas projektowania tych podkładek niezwykle istotne są detale techniczne, a ich rysunki techniczne przedstawiają wymiary oraz kształty, które mają wpływ na funkcjonalność w konkretnych zastosowaniach. Właściwy dobór podkładek jest kluczowy dla efektywności połączeń, co z kolei przekłada się na niezawodność i trwałość całej konstrukcji.
Jakie typy podkładek sprężystych można znaleźć?
Podkładki sprężyste dostępne są w różnych wersjach, z których każda ma swoje unikalne zastosowanie oraz charakterystyki. Do najbardziej rozpoznawalnych należy podkładka DIN 127, która występuje w dwóch wariantach:
- A,
- B, różniących się wysokością.
Innym interesującym typem są podkładki ząbkowane, takie jak modele DIN 6797J oraz DIN 6797V, które dzięki zębom na krawędziach lepiej trzymają się na miejscu. W ofercie znajdują się także:
- podkładki kuliste,
- stożkowe,
- klinowe,
- podkładki dwuotworowe, idealne do zastosowań wymagających ścisłego dopasowania pod obciążeniem.
Z kolei podkładki zębate, na przykład MB i MBL, znacząco zwiększają bezpieczeństwo połączeń w trudnych warunkach. Natomiast podkładki okrągłe uznawane są za najbardziej wszechstronne i wykorzystywane w licznych gałęziach przemysłu oraz budownictwa. Wszystkie wymienione typy podkładek sprężystych wytwarzane są zgodnie z rygorystycznymi normami, co gwarantuje ich wysoką jakość i niezawodność w różnych warunkach pracy.
Jakie materiały używane do produkcji podkładek sprężystych?
Produkcja podkładek sprężystych opiera się na wyborze odpowiednich materiałów, które są dostosowane do specyficznych wymagań wytrzymałościowych i odporności na korozję. Wśród najczęściej wykorzystywanych znajduje się:
- stal sprężynowa, idealna do konstrukcji wystawionych na luzowanie,
- stal nierdzewna A2 (INOX) – jej wysoka odporność na korozję sprawia, że doskonale sprawdza się w wilgotnych i agresywnych warunkach,
- stal kwasoodporna A4 oraz stal nierdzewna DUPLEX (1.4462) – najchętniej wybierane do zastosowań w przemyśle chemicznym oraz farmaceutycznym,
- stal nierdzewna 302, która wyróżnia się dobrą odpornością na ozon i różne chemikalia.
W procesie produkcji dużą wagę przykłada się również do jakości drutu sprężynowego, który charakteryzuje się znakomitymi właściwościami sprężystymi i wytrzymałościowymi, niezbędnymi do zapewnienia efektywności w połączeniach śrubowych. Dzięki zastosowaniu tych zaawansowanych materiałów, podkładki sprężyste zapewniają nie tylko optymalne działanie, ale też długowieczność w różnorodnych aplikacjach przemysłowych.
Jak produkcja podkładek sprężystych wpływa na ich wytrzymałość?
Produkcja podkładek sprężystych ma ogromne znaczenie dla ich trwałości. Kluczowe materiały, takie jak stal sprężynowa, przechodzą przez skomplikowany proces obróbki cieplnej, który znacząco zwiększa ich elastyczność oraz odporność na deformacje. Ta procedura wzmacnia właściwości podkładek, co jest niezbędne w różnych warunkach eksploatacyjnych.
Aby zabezpieczyć je przed korozją, wykorzystuje się różnorodne powłoki ochronne, w tym:
- ocynk galwaniczny,
- ocynk ogniowy,
- ocynk płatkowy, takie jak dacromet czy geomet.
Te technologie są kluczowe, aby wydłużyć żywotność produktu, zwłaszcza w środowiskach o wysokiej wilgotności lub wystawionych na działanie substancji chemicznych. Dzięki nowoczesnym metodom produkcji oraz rygorystycznemu nadzorowi jakości, podkładki sprężyste w pełni odpowiadają ustalonym normom wytrzymałościowym.
Ich wyjątkowe właściwości sprężyste sprzyjają efektywnemu przewodzeniu i niwelowaniu obciążeń mechanicznych, co z kolei minimalizuje ryzyko luzowania w połączeniach. Analizując procesy wytwórcze, można zauważyć, że każdy etap ma decydujący wpływ na ogólną jakość podkładek. To szczególnie istotne w zastosowaniach przemysłowych, gdzie niezawodność i długotrwałość są kluczowe.
Jakie właściwości mają podkładki DIN 127 i PN 82008?
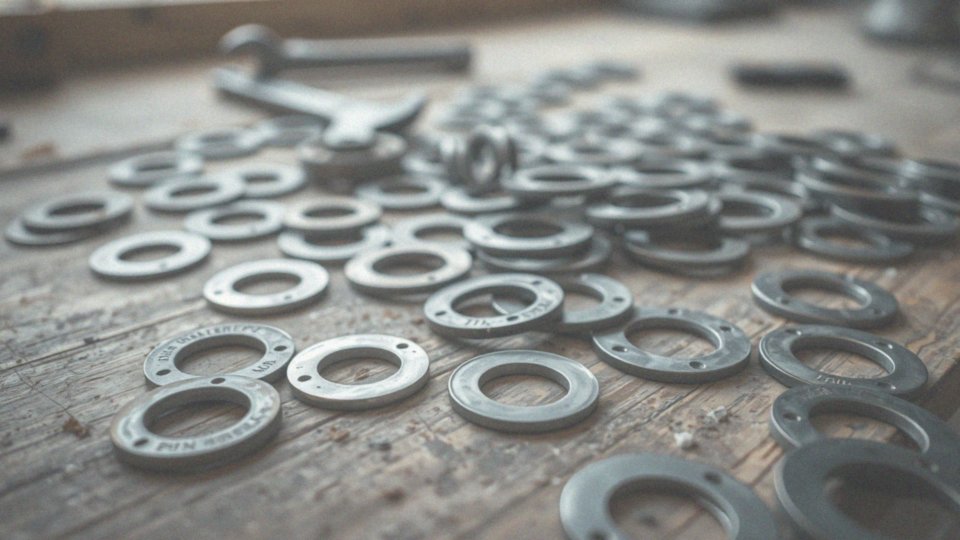
Podkładki DIN 127 i PN 82008 wyróżniają się dużą elastycznością, co przekłada się na ich wytrzymałość i niezawodność. Wykonane z materiałów najwyższej jakości stalowych, są odporne na korozję, co sprawia, że mogą być stosowane w różnych środowiskach.
Te sprężyste elementy stabilizują połączenia śrubowe, skutecznie dostosowując się do zmieniających się obciążeń i eliminując luzowanie się komponentów. Normy DIN 127 oraz PN 82008 precyzują standardy ich produkcji, co zapewnia ich szerokie zastosowanie w sektorze:
- motoryzacyjnym,
- maszynowym,
- budowlanym.
Podkładki zgodne z normą PN 82008 są polskim odpowiednikiem danych z DIN 127, co potwierdza ich wysoką jakość oraz zdolność spełniania wymagań wytrzymałościowych. Ich kluczową rolą jest wsparcie konstrukcji, co znacząco wpływa na stabilność oraz bezpieczeństwo połączeń. Dzięki swojej budowie, te podkładki efektywnie absorbują drgania, co ma fundamentalne znaczenie dla trwałości konstrukcji inżynieryjnych.
Wykorzystanie sprężystych podkładek nie tylko wydłuża żywotność połączeń, ale także redukuje ryzyko uszkodzeń maszyn oraz instalacji, co jest niezwykle ważne dla bezpieczeństwa operacyjnego.
Jakie wymiary mają podkładki sprężyste?
Wymiary podkładek sprężystych mają kluczowe znaczenie dla ich prawidłowego funkcjonowania. Standardy takie jak DIN 127 oraz PN 82008 precyzyjnie definiują niezbędne parametry, w tym średnice:
- wewnętrzną (d1) mieszczącą się w przedziale od 6 mm do 100 mm,
- zewnętrzną (d2), która jest zazwyczaj nieco większa o 2-3 mm,
- grubość (s) waha się od 0,5 mm do 5 mm,
- wysokość, która różni się w zależności od klasy podkładki – A lub B.
Ważnym aspektem jest również fakt, iż wysokość podkładek typu A jest większa w porównaniu do typu B, co sprzyja lepszemu dopasowaniu. Normy te określają również tolerancje wymiarowe, co jest niezbędne dla właściwego łączenia różnych elementów. Troska o te szczegóły jest istotna dla zapewnienia jakości oraz bezpieczeństwa połączeń. Dzięki dokładnym wytycznym, podkładki sprężyste są w stanie sprostać różnorodnym wymaganiom mechanicznym oraz eksploatacyjnym w różnych branżach przemysłu.
Jakie normy dotyczą podkładek sprężystych?
Podkładki sprężyste są regulowane przez szereg norm, które precyzują ich wymiary, charakterystyki mechaniczne oraz materiały wykorzystane w produkcji. Wśród najistotniejszych dokumentów wymienia się:
- DIN 127 (wersje A i B) oraz PN 82008, które określają kluczowe parametry elastyczności i odporności na zmęczenie,
- DIN 6796, koncentrujący się na podkładkach używanych w połączeniach śrubowych, co zapewnia ich stabilność i redukuje ryzyko luzowania,
- DIN 7980, dotyczący podkładek przeznaczonych dla śrub z łbem walcowym, co ma znaczenie w pewnych specyficznych zastosowaniach,
- DIN 6798 oraz DIN 6797, obejmujące podkładki ząbkowane, które zwiększają przyczepność i stabilność nawet w trudnych warunkach.
Normy te są niezbędne, aby podkładki sprężyste osiągały wymagany poziom jakości, co jest istotne w wielu branżach, takich jak motoryzacja, inżynieria maszynowa czy budownictwo. Każda z tych norm precyzuje stosowane wymiary, tolerancje oraz właściwości materiałowe, co z kolei gwarantuje niezawodność i trwałość połączeń. Przestrzeganie tych standardów ma zasadnicze znaczenie dla skutecznej ochrony przed luzowaniem i zapewnienia stabilności mechanizmów w różnorodnych zastosowaniach.
Jakie zastosowanie mają podkładki sprężyste w przemyśle?
Podkładki sprężyste znajdują zastosowanie w wielu sektorach przemysłowych, takich jak:
- budownictwo,
- motoryzacja,
- elektronika.
Ich podstawowa funkcja polega na zapobieganiu luzowaniu połączeń śrubowych, które często są narażone na drgania oraz zmiany obciążeń. Dzięki swojej konstrukcji doskonale radzą sobie w trudnych warunkach, efektywnie redukując wibracje, co stabilizuje połączenia i minimalizuje ryzyko ich uszkodzenia.
W przypadku motoryzacji podkładki odgrywają kluczową rolę w:
- silnikach,
- zawieszeniach,
- systemach, gdzie istotna jest integralność mechaniczna.
Z kolei w budownictwie pełnią funkcję ochronną dla konstrukcji stalowych, chroniąc je przed negatywnym wpływem drgań. W elektronice zapewniają niezawodność połączeń, co jest niezwykle istotne dla prawidłowego funkcjonowania urządzeń.
Podkładki te wykonane są z różnych materiałów, takich jak stal nierdzewna, co sprawia, że charakteryzują się odpornością na korozję. To sprawia, że doskonale sprawdzają się w wymagających warunkach. W rezultacie sprężyste podkładki znacząco przyczyniają się do wydłużenia żywotności połączeń oraz zwiększenia bezpieczeństwa w pracy w różnych branżach.
Dodatkowo, ich właściwości pozwalają na oszczędności związane z czasem i kosztami utrzymania oraz wymiany uszkodzonych elementów.
Jak podkładki sprężyste zapobiegają luzowaniu w połączeniach?
Podkładki sprężyste stanowią efektywne rozwiązanie w walce z luzowaniem połączeń śrubowych. Dzięki swojej elastyczności, są w stanie zrekompensować dynamiczne obciążenia oraz drgania. Funkcjonują niczym sprężyny, co pozwala utrzymać stałą siłę docisku między złącznymi elementami, a tym samym minimalizować ryzyko rozluźnienia.
Wykonane ze stali sprężynowej, doskonale sprawdzają się w warunkach, gdzie występują:
- znaczne obciążenia,
- wibracje.
Gdy połączenie narażone jest na zmienne siły, podkładka adaptuje się, co pozwala na zachowanie stabilności. Nawet w intensywnie drgających środowiskach czy w miejscach o dużej dynamice, te podkładki skutecznie ograniczają luźne połączenia.
Dodatkowo, właściwości materiałowe podkładek sprężystych mają kluczowe znaczenie dla ich trwałości oraz odporności na wibracje. Stosowanie ich w przemyśle jest niezwykle istotne dla bezpieczeństwa oraz niezawodności konstrukcji. W sytuacjach, gdy wymagana jest długoterminowa i bezpieczna instalacja, jakość podkładek ma bezpośredni wpływ na efektywność całego systemu.
Odpowiednio dobrane podkładki sprężyste nie tylko chronią przed luzowaniem, lecz także zapobiegają ewentualnym uszkodzeniom złączek, co jest szczególnie ważne w kontekście długotrwałego użytkowania.
Jakie są korzyści z używania podkładek sprężystych w połączeniach śrubowych?
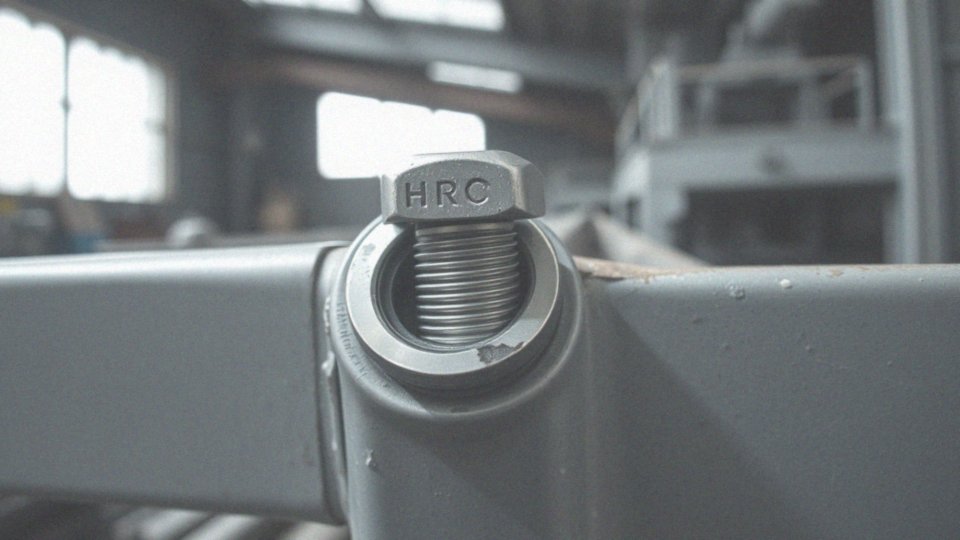
Wykorzystanie podkładek sprężystych w połączeniach śrubowych przynosi szereg korzyści, które znacząco podnoszą trwałość i niezawodność konstrukcji. Przede wszystkim, ich kluczową cechą jest zdolność do zapobiegania luzowaniu się elementów złącznych, co ma szczególne znaczenie w miejscach narażonych na drgania oraz zmienne obciążenia. Te podkładki funkcjonują niczym elastyczne sprężyny, które dostosowują się do dynamicznych sił, co utrzymuje stabilność docisku.
Zastosowanie sprężystych podkładek również chroni powierzchnie łączonych elementów przed uszkodzeniami, co znacząco wydłuża żywotność połączeń oraz obniża koszty związane z ich konserwacją. Co więcej, ich właściwości sprężyste wspierają efektywne przewodzenie obciążeń oraz tłumienie drgań, co ma kluczowe znaczenie w takich branżach, jak:
- motoryzacja,
- budownictwo,
- inżynieria maszynowa.
Dzięki podkładkom sprężystym konstrukcje stają się bardziej stabilne i odporne na długotrwałe zmiany, co zapewnia większe bezpieczeństwo w trakcie operacji mechanicznych. W efekcie, te podkładki odgrywają istotną rolę w zapewnieniu niezawodności połączeń śrubowych, co z kolei przyczynia się do zwiększenia efektywności oraz bezpieczeństwa całych systemów.
Jakie są różnice pomiędzy podkładkami sprężystymi a innymi rodzajami podkładek?
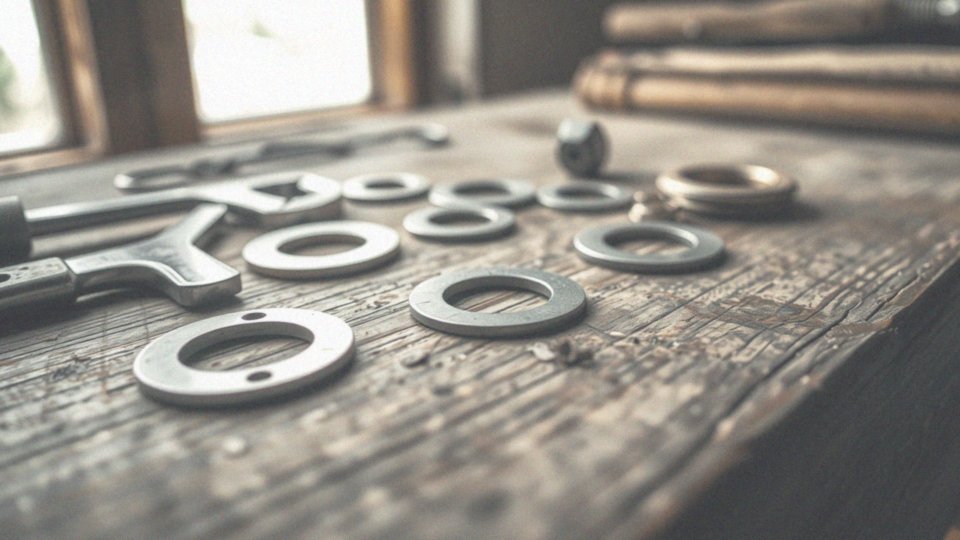
Podkładki sprężyste wyróżniają się na tle innych rodzajów podkładek, takich jak:
- płaskie,
- ząbkowane,
- stożkowe.
Ich kluczowa rola polega na działaniu jako elementy sprężynujące, co pozwala im skutecznie niwelować drgania oraz chronić gwintowane połączenia przed luzowaniem. W odróżnieniu od podkładek płaskich, które jedynie zwiększają powierzchnię docisku, sprężyste zapewniają dynamikę i elastyczność. To właśnie ta cecha sprawia, że sprawdzają się lepiej w warunkach narażonych na wibracje.
Podkładki ząbkowane, z ostrymi krawędziami, lepiej utrzymują się na miejscu, jednak nie mają właściwości sprężynowych. Z kolei podkładki stożkowe są używane w specyficznych zastosowaniach, gdzie istotne jest odpowiednie kątowanie elementów.
Często produkowane są z wysokiej jakości stali sprężynowej lub nierdzewnej, co nadaje im dużą odporność na korozję oraz wyjątkową trwałość. Ich sprężynująca funkcja sprawia, że są niezastąpione w efektywnym zarządzaniu obciążeniami i drganiami w połączeniach mechanicznych.
Jak rysunki techniczne odnoszą się do produkcji podkładek sprężystych?
Rysunki techniczne odgrywają niezwykle ważną rolę w produkcji podkładek sprężystych, ponieważ dostarczają wszystkich istotnych informacji niezbędnych do ich właściwej konstrukcji. Zawierają szczegóły dotyczące:
- wymiarów,
- tolerancji,
- używanych materiałów.
To umożliwia precyzyjne wytwarzanie elementów. Ponadto, są fundamentem, na którym opiera się projektowanie adekwatnych narzędzi i maszyn, istotnych w procesie produkcyjnym. Dzięki specyfikacjom umieszczonym na rysunkach, kontrola jakości gotowych podkładek staje się znacznie łatwiejsza. Odpowiednie tolerancje i oznaczenia są kluczowe dla efektywności tych elementów w różnych połączeniach. Dzięki precyzji rysunków technicznych, produkcja odbywa się zgodnie z normami, takimi jak DIN 127 czy PN 82008, co wpływa na trwałość oraz bezpieczeństwo ich zastosowań.
Co więcej, dokumentacja techniczna ułatwia współpracę między różnymi etapami produkcji, co z kolei zwiększa efektywność wszystkich procesów wytwórczych. W sytuacji, gdy zachodzi potrzeba wprowadzenia modyfikacji wymiarów, rysunek techniczny staje się bezpośrednim punktem odniesienia dla wszystkich działów zajmujących się produkcją i kontrolą jakości. Dzięki temu każdy wyprodukowany element odpowiada wymaganiom funkcjonalności, co ma istotny wpływ na ogólną niezawodność i wydajność systemów, w których podkładki sprężyste są wykorzystywane.