Spis treści
Jakie są rodzaje podkładek pod śruby?
Podkładki pod śruby występują w różnych wariantach, co wynika z ich przeznaczenia oraz metody wykonania. Na przykład:
- podkładki płaskie – świetne rozwiązanie dla uzyskania równych połączeń śrubowych,
- podkładki zabezpieczające – skutecznie hamują luzowanie się śrub, co jest kluczowe w wielu zastosowaniach,
- podkładki sprężynowe – idealne dla elastyczności i odporności na wstrząsy,
- podkładki uszczelniające – chronią przed wyciekami, co czyni je szczególnie przydatnymi w instalacjach hydraulicznych,
- podkładki barkowe, nylonowe oraz kołnierzowe – mają swoje specyficzne cechy oraz zastosowania, zwiększając efektywność połączeń w różnych branżach.
Dzięki temu można je dostosować do wielu różnorodnych potrzeb, co podnosi jakość wykonywanych prac.
Jak podkładki pod śruby dzielą się na różne typy?
Podkładki pod śruby występują w wielu wariantach, z których każdy pełni specyficzną rolę w połączeniach. Przykładowo:
- podkładki płaskie pomagają w równomiernym rozłożeniu sił, co sprzyja stabilności całego połączenia,
- podkładki zabezpieczające skutecznie eliminują ryzyko luzowania elementów mocujących, co jest szczególnie istotne w aplikacjach narażonych na wibracje, takich jak silniki czy maszyny,
- podkładki sprężyste, znane również jako sprężynowe, działają jak amortyzatory, utrzymując odpowiednie napięcie w połączeniach i skutecznie absorbując wstrząsy,
- podkładki uszczelniające łączą zalety podkładek płaskich z funkcją uszczelniania, co sprawia, że są niezastąpione w hydraulice, gdzie zapobieganie wyciekom jest kluczowe,
- podkładki izolowane oferują ochronę przed korozją oraz przewodnictwem elektrycznym,
- podkładki regulacyjne umożliwiają precyzyjne dostosowanie wysokości połączenia,
- podkładki kołnierzowe, barkowe oraz nylonowe mają unikalne właściwości, idealnie odpowiadające różnorodnym potrzebom w różnych dziedzinach przemysłu.
Dzięki temu, każdy rodzaj podkładki przyczynia się do zwiększenia trwałości i efektywności połączeń.
Jakie materiały są wykorzystywane do produkcji podkładek?
Produkcja podkładek opiera się na różnych surowcach, co umożliwia ich wszechstronne zastosowanie w różnych sektorach. Najczęściej spotykane materiały to:
- stal, w szczególności jej wersje nierdzewna A2 oraz kwasoodporna, wyróżnia się wyjątkową odpornością na obciążenia, przez co podkładki stalowe doskonale sprawdzają się w miejscach narażonych na duże siły oraz wibracje,
- miedź, dzięki swoim rewelacyjnym właściwościom przewodzenia zarówno elektryczności, jak i ciepła, jest nieoceniona tam, gdzie te cechy są niezwykle istotne,
- aluminium, które jest lekkie oraz odporne na korozję, stanowi świetny wybór dla aplikacji w branży motoryzacyjnej i lotniczej,
- tworzywa sztuczne, takie jak PVC, poliamid, nylon czy PTFE, cieszą się dużym uznaniem. Ich lekkość oraz odporność na różnorodne chemikalia sprawiają, że chętnie wybierane są w trudnych warunkach.
Decyzja o wyborze odpowiedniego materiału zawsze powinna być dostosowana do specyfiki danego zastosowania, co ma kluczowe znaczenie dla trwałości i efektywności połączeń.
Co charakteryzuje podkładki metalowe?
Podkładki metalowe wyróżniają się doskonałą odpornością na intensywne obciążenia oraz trudne warunki atmosferyczne, co czyni je nieocenionymi w wielu dziedzinach. Najczęściej wytwarzane są ze stali oraz stali nierdzewnej, co gwarantuje ich długotrwałość i odporność na korozję. W zależności od specyficznych wymagań, mogą być także wykonane z aluminium czy miedzi.
Różnorodność rozmiarów podkładek pozwala na ich precyzyjne dopasowanie do śrub oraz schematów montażowych, co znacząco wpływa na ich przydatność. Lekka konstrukcja i prostota montażu dodatkowo zwiększają efektywność przeprowadzanej instalacji.
W kontekście połączeń śrubowych, podkładki odgrywają fundamentalną rolę, gwarantując stabilność oraz efektywność całej konstrukcji. Jest to szczególnie istotne w sytuacjach, w których występują wibracje bądź poważne obciążenia. Oprócz podstawowych funkcji, podkładki metalowe stabilizują połączenia, co skutkuje znacznym zmniejszeniem ryzyka luzowania.
Ich szerokie zastosowanie w takich sektorach jak motoryzacja, budownictwo czy przemysł świadczy o ich wszechstronności oraz kluczowym znaczeniu dla zapewnienia jakości i bezpieczeństwa.
Co to są podkładki uszczelniające i jak działają?
Podkładki uszczelniające to niezwykle ważne komponenty, które skutecznie chronią połączenia śrubowe przed wnikaniem wody i innych substancji. Ich zasadnicza rola polega na idealnym przyleganiu do montowanych powierzchni, co znacząco zwiększa odporność na korozję oraz zabezpiecza przed ewentualnymi uszkodzeniami.
Dzięki nim, połączenia zachowują trwałość, co jest szczególnie istotne w wilgotnych oraz agresywnych chemicznie środowiskach. Znalazły szerokie zastosowanie w różnych branżach, takich jak:
- hydraulika,
- motoryzacja.
W tych dziedzinach niezawodność połączeń odgrywa kluczową rolę. Produkowane są z materiałów, które wykazują dużą odporność na działanie chemikaliów, co znacząco podnosi ich efektywność w trudnych warunkach. Wykorzystując te podkładki, można znacznie obniżyć ryzyko przecieków, zapewniając jednocześnie optymalną ochronę dla elementów połączeniowych.
Jakie są funkcje podkładek zabezpieczających?
Podkładki zabezpieczające odgrywają kluczową rolę w utrzymaniu stabilności połączeń śrubowych. Ich główne zadanie to ograniczenie ruchomości elementów mocujących, co z kolei zmniejsza ryzyko ich luzowania, szczególnie w sytuacjach, gdy występują drgania i obciążenia. Dzięki nim mocowania stają się bardziej trwałe, co jest niezwykle istotne w takich branżach jak:
- motoryzacja,
- budownictwo.
W przypadku połączeń narażonych na wibracje, te podkładki skutecznie ograniczają ruch zarówno śrub, jak i nakrętek, co zapobiega ich przypadkowemu odkręcaniu. Dodatkowo, stabilizacja konstrukcji minimalizuje ryzyko awarii spowodzonej luzowaniem. Zastosowanie podkładek zabezpieczających nie tylko poprawia jakość montażu, ale także wydłuża żywotność mechanizmów, w których są one używane. Szeroki wybór dostępnych na rynku podkładek sprawia, że łatwo można je zintegrować w różnych projektach. Na przykład, podkładki sprężynowe oferują dodatkowe właściwości amortyzujące, a w połączeniu z innymi typami podkładek mogą znacznie poprawić efektywność oraz trwałość połączeń śrubowych.
Jakie są zalety podkładek sprężystych?
Podkładki sprężyste, zwane również sprężynowymi, odgrywają kluczową rolę w stabilnym mocowaniu różnych elementów. Ich elastyczność pozwala na efektywne pochłanianie wstrząsów, co znacząco przyczynia się do trwałości połączeń, zwłaszcza w warunkach zmiennego obciążenia. Jedną z ich najważniejszych zalet jest zapobieganie luzowaniu się łączeń, co ma ogromne znaczenie w miejscach narażonych na intensywne wibracje, jak na przykład w:
- motoryzacji,
- przemyśle.
Te podkładki dbają o odpowiednie napięcie, które z kolei wpływa na bezpieczeństwo i niezawodność całego systemu. Dzięki swej wszechstronności, mogą być stosowane zarówno w tradycyjnych połączeniach metalowych, jak i w konstrukcjach, które muszą znosić zmienne warunki atmosferyczne. W ten sposób ograniczają ryzyko uszkodzeń mechanicznych i podnoszą efektywność całego montażu. Dodatkowo, należy podkreślić, że podkładki sprężyste nie tylko zapewniają stabilność, ale również długoterminową niezawodność. Z tego powodu są niezastąpione w wielu gałęziach przemysłu.
Jakie zastosowanie mają podkładki wyrównujące?
Podkładki wyrównujące odgrywają kluczową rolę w połączeniach śrubowych, umożliwiając uzyskanie stabilnych i równych złączy. Dzięki nim nierówności powierzchni elementów mocowanych można z łatwością zniwelować, co jest szczególnie istotne podczas montażu na nierównych fundamentach. Dzięki poprawie kąta montażu odbywa się efektywne rozłożenie siły, co znacząco zwiększa stabilność całej konstrukcji.
Ich zastosowanie jest również niezwykle ważne, gdy chodzi o:
- minimalizowanie różnic w wysokości pomiędzy elementami,
- poprawę jakości oraz bezpieczeństwa połączeń.
W wielu dziedzinach, takich jak budownictwo czy inżynieria mechaniczna, użycie tych podkładek jest nieocenione. Stabilizują one połączenia i podnoszą efektywność montażu, co ma duże znaczenie w sytuacjach narażonych na wibracje czy zmienne obciążenia. W efekcie, ich zastosowanie może znacznie wydłużyć trwałość oraz niezawodność połączeń, co czyni je niezwykle wartościowym rozwiązaniem w różnych zastosowaniach przemysłowych.
Jakie różnice są między podkładkami okrągłymi a kwadratowymi?
Podkładki, zarówno okrągłe, jak i kwadratowe, różnią się nie tylko kształtem, ale również funkcjonalnością. Okrągłe podkładki często znajdują zastosowanie w standardowych połączeniach, ponieważ równomiernie rozkładają nacisk, co czyni je niezwykle popularnymi w budownictwie oraz mechanice. Z kolei kwadratowe podkładki wyróżniają się większą powierzchnią przylegania, co sprawia, że są doskonałym wyborem w przypadkach, które wymagają lepszej stabilności lub muszą dostosować się do różnych kształtów.
Wykorzystanie podkładek obejmuje:
- specjalistyczne konstrukcje,
- lepszą stabilność,
- ścisłe przyleganie do płaskiej powierzchni.
Decyzja dotycząca wyboru między okrągłym a kwadratowym modelem ma duże znaczenie dla efektywności połączeń. Dobrze dobrane podkładki mogą znacznie zwiększyć odporność na luzowanie, dlatego kluczowe jest uwzględnienie specyfiki zastosowania oraz rodza… obciążeń, które będą na nie działać.
Jakie znaczenie mają normy jakościowe DIN i ISO dla podkładek?
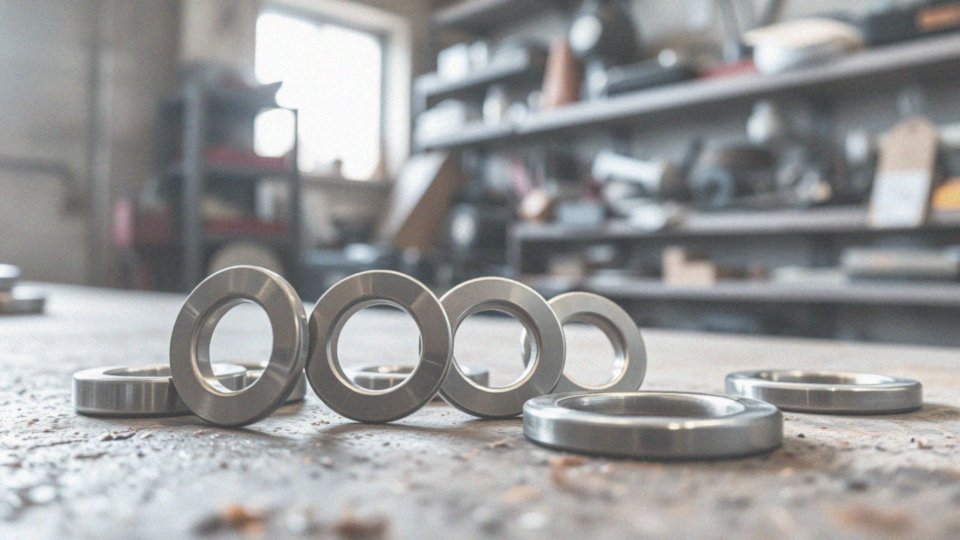
Normy jakościowe DIN i ISO stanowią fundament w procesie produkcji podkładek. Określają one kluczowe wytyczne dotyczące:
- materiałów,
- wymiarów,
- wytrzymałości elementów.
Dzięki tym regulacjom produkowane podkładki osiągają wysoki poziom jakości i niezawodności. Na przykład, normy DIN 125 oraz ISO 7089 dotyczą bezpośrednio płaskich podkładek, co podkreśla ich znaczenie w kontekście zgodności z przemysłowymi standardami. Produkty wytwarzane według tych norm ukazują niezwykłą trwałość i odporność na różne obciążenia, co przyczynia się do zwiększenia bezpieczeństwa połączeń śrubowych.
Minimalizują one ryzyko uszkodzeń czy luzowania, co ma szczególne znaczenie w warunkach dużych drgań. Badania wskazują, że aż 70% awarii w mechanicznych połączeniach związanych jest z brakiem zgodności podkładek z normami. Te regulacje wymuszają na producentach wdrażanie określonych technik produkcji oraz rygorystyczną kontrolę jakości, co przekłada się na uzyskanie lepszych parametrów użytkowych tych elementów.
Dodatkowo, podkładki, które spełniają surowe wymagania norm, łatwo integrują się z innymi komponentami, co znacząco poszerza ich zastosowanie w rozmaitych branżach, takich jak budownictwo, motoryzacja i przemysł lotniczy.
Jak podkładki pod śruby zapobiegają luzowaniu się połączeń?
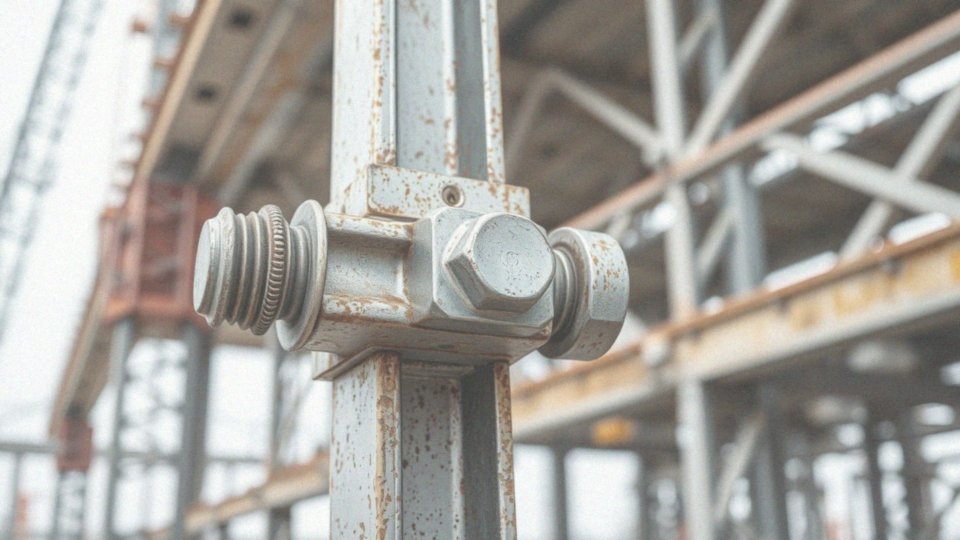
Podkładki pod śruby odgrywają niezwykle istotną rolę w zapobieganiu luzowaniu się połączeń. Znajdują zastosowanie w wielu dziedzinach, w tym w budownictwie i motoryzacji. Ich działanie polega na zwiększeniu powierzchni kontaktu pomiędzy śrubą a materiałem, co skutkuje minimalizowaniem ryzyka odkształceń oraz luzów.
Różnego rodzaju podkładki zabezpieczające, takie jak:
- sprężynowe,
- korkowe,
- plastikowe.
Stabilizują połączenia i ograniczają ruchomość nakrętek oraz śrub. W ten sposób efektywnie zapobiegają ich przypadkowemu odkręcaniu się, które może być spowodowane drganiami oraz obciążeniami. Użycie tych elementów jest szczególnie zalecane w środowiskach, gdzie występują intensywne wibracje, jak w silnikach czy maszynach przemysłowych.
Dzięki wyborowi odpowiednich materiałów, takich jak:
- stal nierdzewna,
- tworzywa sztuczne.
Trwałość połączeń znacząco się zwiększa, a ich odporność na korozję oraz trudne warunki atmosferyczne wpływa na długowieczność instalacji. Starannie dobrane podkładki mogą znacząco wydłużyć czas eksploatacji oraz zredukować ryzyko awarii. Ma to kluczowe znaczenie w inżynierii mechanicznej oraz innych sektorach, gdzie jakość i bezpieczeństwo połączeń są priorytetowe.
W jakich sytuacjach wykorzystuje się podkładki z tworzyw sztucznych?
Podkładki wykonane z tworzyw sztucznych znajdują szerokie zastosowanie w różnych dziedzinach. Z łatwością można je wykorzystać tam, gdzie istotne są:
- niska waga,
- odporność na korozję,
- właściwości izolacyjne.
Dzięki tym atutom idealnie sprawdzają się w trudnych warunkach, jak wilgotne środowiska czy obszary narażone na działanie substancji chemicznych. Na przykład, w instalacjach elektrycznych chronią przed niepożądanym przewodnictwem prądu między metalowymi komponentami. W branży motoryzacyjnej i budowlanej skutecznie zapobiegają korozji galwanicznej, co jest kluczowe podczas łączenia różnych metali.
Tworzywa takie jak PVC, poliamid czy nylon wykazują dużą odporność na substancje chemiczne, co znacznie zwiększa ich trwałość w wymagających warunkach. Kiedy są stosowane w miejscach narażonych na obciążenia mechaniczne, zachowują swoje właściwości, co czyni je niezwykle funkcjonalnymi.
W zestawieniu z metalowymi odpowiednikami, podkładki z tworzyw sztucznych znacząco obniżają wagę całej konstrukcji. Jest to szczególnie istotne w projektach, gdzie liczy się każdy gram. Dzięki tym właściwościom podkładki te w znaczący sposób przyczyniają się do efektywności i bezpieczeństwa różnorodnych połączeń w przemyśle.
Jakie obciążenia wytrzymują różne rodzaje podkładek?
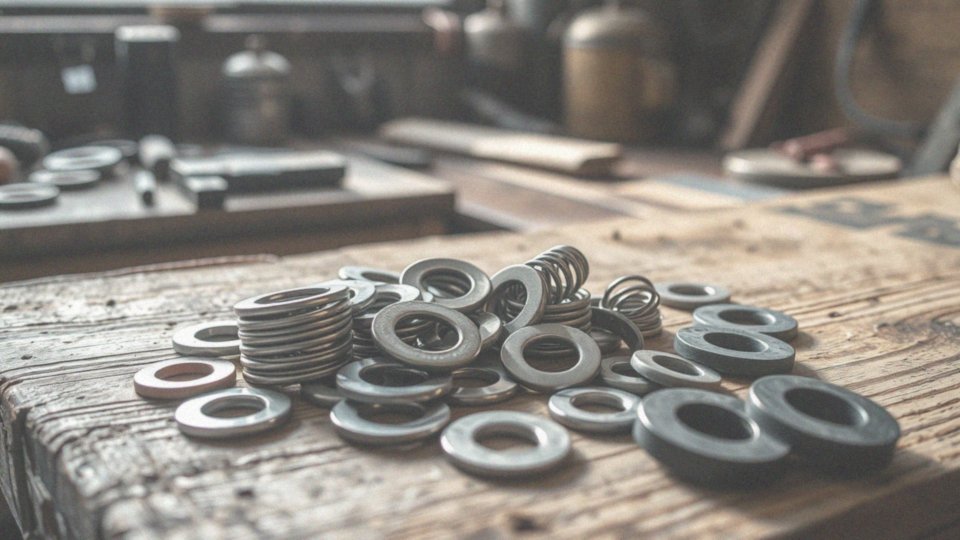
Wytrzymałość podkładek pod śruby jest ściśle związana z ich typem oraz materiałem, z którego zostały wykonane. Metalowe podkładki, zwłaszcza ze stali, charakteryzują się znaczną odpornością na różnorodne obciążenia, zarówno te statyczne, jak i dynamiczne. Dzięki temu doskonale sprawdzają się w ekstremalnych warunkach, gdzie siły działające na nie są znaczne.
Podkładki sprężyste, zaprojektowane do pracy w zmieniających się warunkach obciążeniowych i drgań, skutecznie amortyzują wstrząsy, co przyczynia się do wydłużenia trwałości połączeń. Z kolei podkładki z tworzyw sztucznych, takich jak PVC czy nylon, doskonale radzą sobie w sytuacjach z lżejszymi obciążeniami. Ich wysoka odporność na korozję sprawia, że są idealnym wyborem tam, gdzie ochrona przed wilgocią i substancjami chemicznymi ma kluczowe znaczenie.
Właściwy wybór rodzaju podkładki powinien opierać się na specyfice łączenia oraz warunkach eksploatacji, co gwarantuje optymalną siłę łączenia. Na przykład:
- podkładki sprężynowe przydają się w aplikacjach, które wymagają elastyczności,
- metalowe podkładki oferują stabilność w trudniejszych sytuacjach.
Bogata różnorodność materiałów i typów podkładek pozwala na ich idealne dopasowanie do konkretnych potrzeb, co jest niezbędne dla efektywności całego systemu.